The Importance of a Prototype Mold Factory in Modern Manufacturing
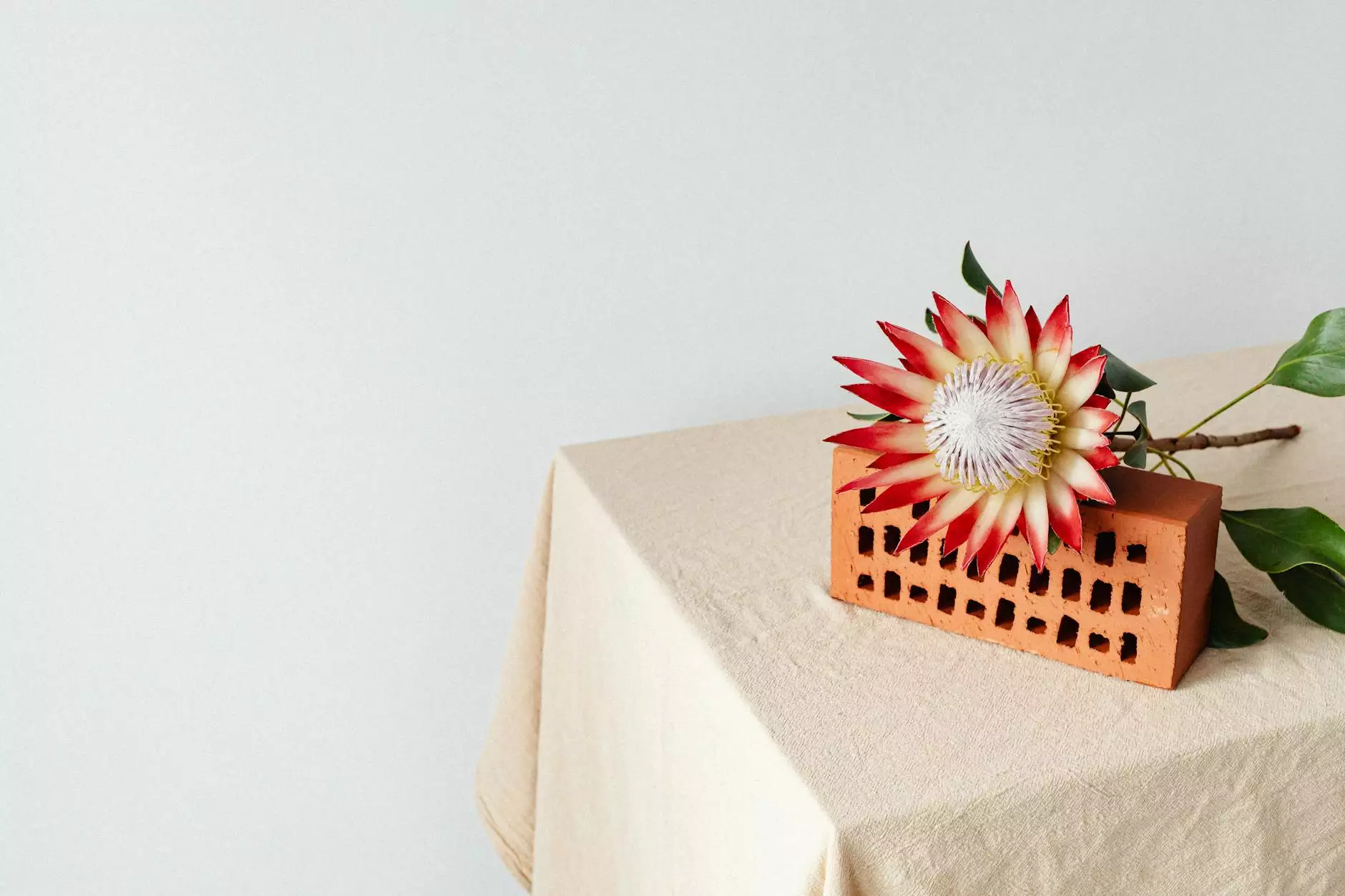
The landscape of manufacturing is continuously evolving, and at the heart of this transformation lies the crucial role of a prototype mold factory. Businesses are no longer satisfied with just bringing a product to market; they strive for excellence, efficiency, and innovation. In this article, we delve into the myriad benefits of having a dedicated prototype mold factory and how it can propel businesses, particularly in the metal fabricators sector, to new heights.
What is a Prototype Mold Factory?
A prototype mold factory specializes in creating molds that can be used for producing prototypes of products before they go into full production. This process is vital for businesses as it allows them to test designs, materials, and functionalities without committing to large-scale manufacturing. The significance of such factories cannot be overstated, especially when it concerns innovation and quality assurance.
Key Functions of a Prototype Mold Factory
- Design Verification: Prototypes allow manufacturers to verify designs and make necessary adjustments before mass production.
- Material Testing: Different materials can be tested for durability and functionality in real-world scenarios.
- Cost Reduction: Identifying issues early in the design phase reduces costs associated with recalls and redesigns.
- Time Efficiency: Shorter production cycles allow for faster market entry and adaptability to consumer demands.
- Enhanced Collaboration: Prototypes facilitate better communication among design teams, stakeholders, and clients.
Advantages of Partnering with a Prototype Mold Factory
Businesses, particularly in the metal fabrication industry, can reap numerous benefits by collaborating with a well-established prototype mold factory. Here’s a closer look at some of these advantages:
1. Accelerated Product Development
The integration of a prototype mold factory into the product development phase significantly speeds up the entire process. Rapid prototyping technologies such as 3D printing and CNC machining reduce the time from concept to prototype. This acceleration allows businesses to respond swiftly to market trends and consumer demands, providing a substantial competitive edge.
2. Increased Product Quality
Prototypes serve as a testing ground for identifying design flaws and functional issues. By addressing these in the prototype stage, businesses can enhance the overall quality of their final products. This focus on quality leads to increased customer satisfaction and loyalty, ultimately driving sales and growth.
3. Cost Efficiency through Iteration
One of the most significant advantages offered by a prototype mold factory is the ability to iterate without incurring substantial costs. By testing various designs and materials, companies can pinpoint the most effective and cost-efficient manufacturing processes. This iterative approach minimizes waste and maximizes resource allocation.
4. Innovation and Customization
Today’s consumers are looking for unique and customized products. A prototype mold factory can facilitate innovation by enabling manufacturers to experiment with innovative designs and materials. This flexibility in the prototyping phase ensures that businesses can meet specific customer needs and preferences, setting them apart from competitors.
5. Risk Mitigation
Investing in new products comes with inherent risks. A prototype mold factory allows companies to identify potential flaws before full-scale production begins. This proactive approach to risk management not only protects investment but also safeguards a company's reputation in the marketplace.
Choosing the Right Prototype Mold Factory
Finding the ideal prototype mold factory is essential for optimizing the prototyping process. Here are critical factors to consider when selecting a partner:
1. Expertise and Experience
Choose a factory that boasts a proven track record in creating prototypes across various industries. Experience in metal fabrication is particularly valuable, as it ensures familiarity with both the materials and production techniques essential for success.
2. Technology and Equipment
State-of-the-art technology and machinery are vital for producing high-quality prototypes. A factory equipped with modern tools will be able to deliver superior prototypes efficiently.
3. Material Variability
The ability to work with a variety of materials is crucial. A factory that utilizes advanced materials, such as composites or specialty metals, will provide more options for prototype creation, thereby increasing innovation opportunities.
4. Customer Support and Collaboration
A good prototype mold factory will emphasize collaboration and communication. Look for partners that offer robust support at every stage of the prototyping process and are willing to work closely with your team to achieve desired outcomes.
5. Quality Assurance Processes
Inquire about the quality assurance processes in place at the factory. High standards of quality control are essential for ensuring that prototypes meet or exceed expectations before moving into production.
Unleashing Creativity Through Prototyping
Prototyping isn’t merely about testing functionality; it’s also a conduit for creativity. Engaging with a prototype mold factory allows engineers and designers to experiment freely, fostering an environment where innovation flourishes. As companies explore new concepts, they inevitably enhance their brand reputation and market position.
Real-World Success Stories
Numerous companies have successfully leveraged prototype mold factories to realize groundbreaking products. A few notable examples include:
- Apple: Known for its innovative designs, Apple often tests various prototypes for their products, refining functionality and aesthetics before release.
- Ford: The automotive giant utilizes prototype mold factories to develop cutting-edge vehicle components, enhancing both performance and safety.
- Dyson: This tech company is renowned for its relentless pursuit of innovation, where prototyping plays a key role in developing its high-performance appliances.
Future Trends in Prototype Mold Factories
The future of prototype mold factories is bright, shaped by advancements in technology and shifting market demands. Here are a few trends to watch for:
1. Automation and Smart Manufacturing
As industries embrace automation, prototype mold factories are expected to integrate smart manufacturing technologies. This will enable faster production cycles and enhanced precision, ultimately leading to superior prototypes.
2. Sustainability Focus
With increasing emphasis on sustainability, many factories are seeking eco-friendly materials and processes. This trend will influence how prototypes are produced, potentially utilizing renewable resources and reducing waste.
3. Advanced Materials Development
The ongoing research into advanced materials will likely be reflected in prototyping processes. Expect to see more factories adopting innovative composites and other materials that enhance product performance and durability.
4. Digital Twin Technology
Digital twin technology, which creates virtual replicas of physical systems, is anticipated to revolutionize the prototyping phase. This technology enables engineers to simulate various scenarios during the design process to ensure optimal outcomes.
Conclusion
The role of a prototype mold factory in today's manufacturing landscape is undeniably significant. It serves as a critical element for businesses aiming to innovate, reduce costs, and assure quality. By fostering collaboration and embracing modern technologies, these factories not only streamline the prototyping process but also empower businesses to thrive in a competitive marketplace. As we look to the future, the continued evolution of prototype mold factories will undoubtedly reshape how industries conceptualize, design, and produce their products.
In summary, tapping into the advantages offered by a dedicated prototype mold factory can position your business for greater success. Emphasize the importance of early testing, flexibility, and innovation to harness the potential of your ideas and transform them into market-leading products.