Understanding Injection Molding Tools: The Backbone of Metal Fabrication
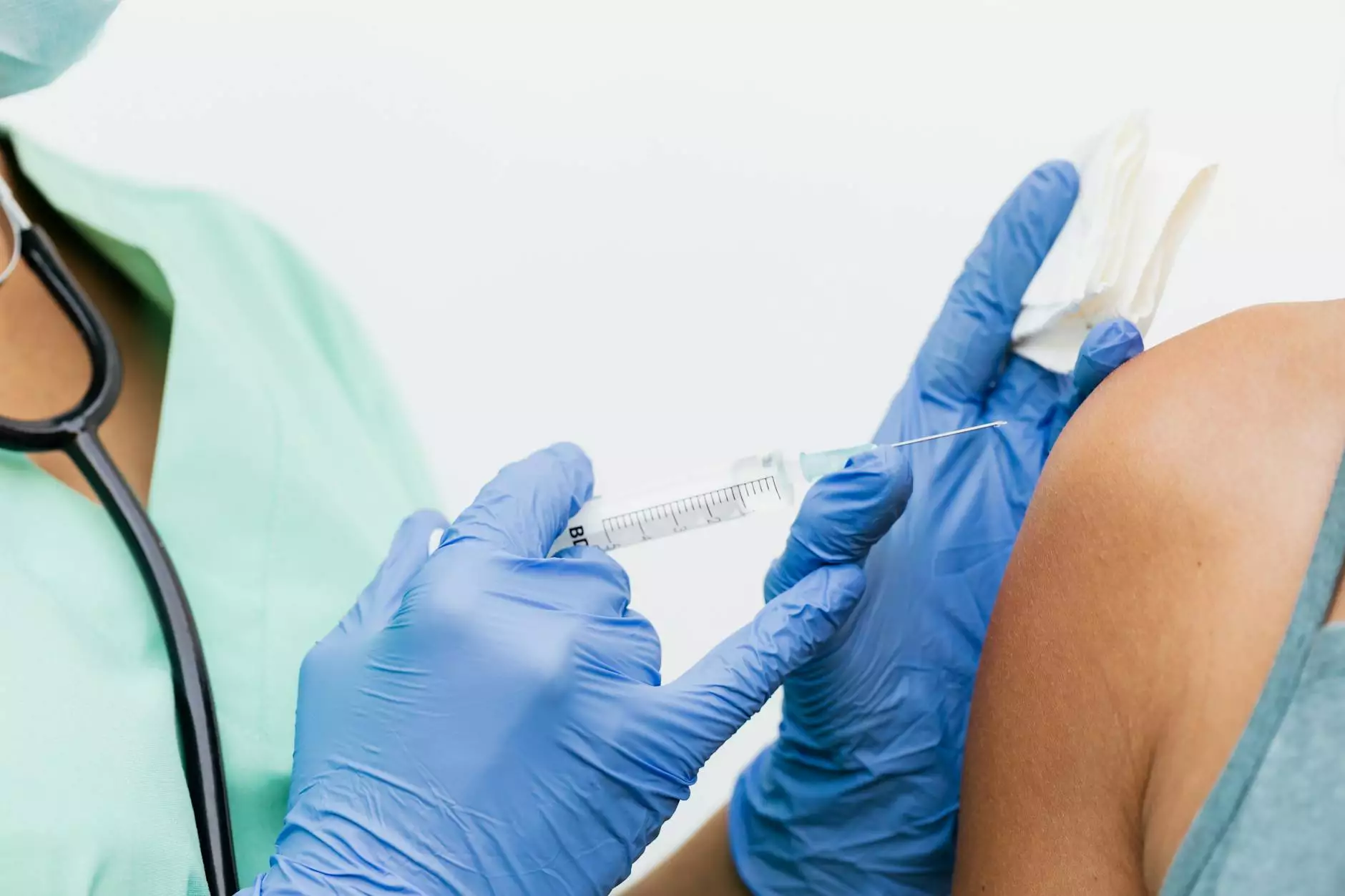
Injection molding tools are crucial components in the realm of metal fabrication, enabling the efficient and precise manufacture of intricate parts used across various industries. As we delve into the significance of these tools, we will explore their functionality, types, and the impact they have on production efficiency.
The Fundamentals of Injection Molding Tools
Injection molding is a manufacturing process used to produce parts by injecting material into a mold. It is particularly well-suited for high-volume production runs. Injection molding tools are the machinery and molds employed to facilitate this process. In metal fabrication, these tools must be designed to endure the rigors of the operation while delivering exceptional precision and surface finish.
Key Components of Injection Molding Tools
- Mold Base: The foundation of the injection mold that supports the components.
- Cavities and Cores: The shapes that define the final part's geometry, crafted with precision to ensure accuracy.
- Injection Unit: The mechanism that melts the metal and injects it into the mold.
- Ejector System: Responsible for removing the completed part from the mold.
- Cooling System: Manages the temperature of the mold to solidify the injected material effectively.
Types of Injection Molding Tools
There are several different types of injection molding tools designed to cater to various needs in metal fabrication:
1. Hot Runner Molds
Hot runner molds are equipped with a heating system that keeps the plastic in a molten state as it travels through the runners. This system reduces waste and enhances the efficiency of the molding process. The heat maintains a consistent temperature, ensuring that the material does not solidify before it reaches the cavities.
2. Cold Runner Molds
With cold runner molds, the runner system is not heated. This means that any leftover material in the runners after injection must be discarded. Although this may lead to some material wastage, cold runner molds are generally simpler and more affordable to manufacture.
3. Multi-Cavity Molds
Multi-cavity molds contain multiple cavities for the same part. This means that multiple units can be produced simultaneously, significantly increasing production efficiency and reducing unit costs. They are often used in high-volume manufacturing where consistency is key.
4. Family Molds
Family molds allow for the production of different parts in a single cycle. This versatility makes them ideal for companies looking to maximize output while minimizing setup time and costs. Each cavity in a family mold can produce a different part, often used for parts that are similar in shape or application.
The Importance of Injection Molding Tools in Metal Fabrication
Injection molding tools play a vital role in the metal fabrication industry. Their importance can be clearly seen in several key areas:
1. Precision and Accuracy
Injection molding tools are renowned for their ability to produce parts with extremely tight tolerances. This precision is critical for components that must fit together seamlessly or that interact with other machine elements. High-quality molds can achieve tolerances of +/- 0.001 inches or better, essential for industries like aerospace and automotive.
2. Cost Efficiency
Investing in high-quality injection molding tools pays off in the long run. Despite the initial costs of creating the molds, the efficiency of the production process and the reduction of material waste can lead to significant savings. High-volume production means that costs per unit decrease, which is a crucial consideration in any competitive manufacturing environment.
3. Versatility
Injection molding tools can be adapted for various products, from complex geometries to simple shapes. This adaptability allows manufacturers to pivot quickly to meet new market demands or to develop innovative products without the need for entirely new equipment.
4. Material Optimization
Advanced injection molding technologies allow for the use of a wide range of materials beyond traditional plastics. Today, manufacturers can use various metal alloys, composites, and other specialized materials within injection molding processes, expanding the potential applications of this technology.
How to Choose the Right Injection Molding Tool
Selecting the right injection molding tool for your production needs involves several considerations:
- Production Volume: Assess whether you are producing high or low volumes, as this impacts the type of mold you should choose.
- Part Complexity: Evaluate the complexity of the parts you intend to produce. More intricate designs may require advanced mold features.
- Material Selection: Different materials require different considerations in mold design, such as the melting temperatures and cooling times.
- Budget: Determine the budget for both initial investments and ongoing maintenance costs.
Challenges in Using Injection Molding Tools
While injection molding presents numerous advantages, it is not without its challenges:
1. Initial Cost
The manufacturing of high-quality injection molding tools can be quite expensive, requiring significant upfront investment. This can be a barrier for startups or small manufacturers.
2. Maintenance and Repair
Maintaining molds and injection machinery is crucial for ensuring ongoing production efficiency. Regular maintenance is necessary to prevent downtime and maintain quality.
3. Design Constraints
Injection molding requires meticulous design considerations, especially regarding draft angles, wall thickness, and other factors that might affect mold release and part quality. Poorly designed molds can lead to production issues and increased costs.
Future Trends in Injection Molding Tools
As technology continues to evolve, so do injection molding tools. Here are some trends that are shaping the future of this vital industry:
1. Automation and Smart Manufacturing
The integration of automation technologies is enhancing the efficiency and reliability of injection molding processes. Smart factories that utilize IoT devices can monitor mold performance in real-time, optimize production schedules, and minimize downtime.
2. Advanced Materials
Ongoing research and development are expanding the range of materials that can be effectively used in injection molding. New metal alloys and composites with enhanced properties are becoming available, allowing for even more innovative applications.
3. Sustainability Practices
With an increasing focus on sustainability, the injection molding industry is exploring recycling options for scrap materials and developing processes that minimize waste and energy consumption.
4. Innovative Mold Designs
The demand for more complex and efficient mold designs is on the rise. This includes improvements in cooling designs, enhanced ejection systems, and modular mold designs that can be adapted for various products and processes.
Conclusion
Injection molding tools are indispensable in the metal fabrication landscape, driving efficiency, cost-effectiveness, and precision in the manufacturing process. Understanding the various types of injection molding tools, their importance, and the current trends can significantly enhance decision-making for manufacturers. Whether improving existing processes or investing in new tooling solutions, appreciating the role of these tools is essential for success in today’s competitive market.
For more information on high-quality injection molding tools, visit DeepMould, where innovation meets precision in manufacturing.